„Die Batterielinie läuft wie ein Uhrwerk“
Seit mittlerweile zehn Jahren verfügt das MEET Batterieforschungszentrum der Universität Münster über eine eigene Batteriepilotlinie. Bestehend aus mehreren Anlagen, ermöglicht sie die eigenständige Produktion von Lithium-Ionen-Batterien im hauseigenen mehrlagigen Pouch-Design (11966) mit Kapazitäten zwischen drei und zehn Amperestunden: vom Anmischen des Slurrys über das Fertigen von Elektroden bis hin zur Zellassemblierung. Anlässlich des Jubiläums schauen wir mit unserem ehemaligen Direktor, Dr. Gerhard Hörpel, und unserem Leiter des Forschungsbereichs System Zelle, Dr. Markus Börner, auf die Anfänge der Batterielinie und ihre stetige Weiterentwicklung zurück und werfen gleichzeitig einen Blick in ihre Zukunft.
Gehen wir zehn Jahre zurück: Wie kam es dazu, dass das MEET eine eigene Batterielinie bekommen hat?
Gerhard Hörpel: Schon während der Planungsphase des Gebäudes für das MEET Batterieforschungszentrum haben Martin Winter und ich das Technikum, das die Batterielinie beherbergt, in das Konzept integriert. Wir wollten von Beginn an auch größere Zellen produzieren können als Knopfzellen. Da entsprechende Produktionsanlagen hierzulande nicht zu erhalten waren, haben mein damaliger MEET Kollege Pascal Noll und ich uns eng mit japanischen und chinesischen Herstellern ausgetauscht. Zu unserem Hauptansprechpartner in Japan, Dr. Kazunori Ozawa, dem damaligen Präsidenten des Zellenherstellers ENAX, hat sich in der Zeit ein enges Vertrauensverhältnis aufgebaut. Als beim Transport aus Fernost Teile der Batterielinie bei einem Schiffsunglück im Meer versunken sind, haben wir also nicht gleich die Köpfe in den Sand gesteckt. Und nur sechs Wochen – und einiges an Blut und Schweiß später – ist die Anlage bei uns angekommen. Kazunori Ozawa und sein Team haben in enger Zusammenarbeit mit dem MEET Technik-Team auch die Inbetriebnahme der Anlage in Münster begleitet.
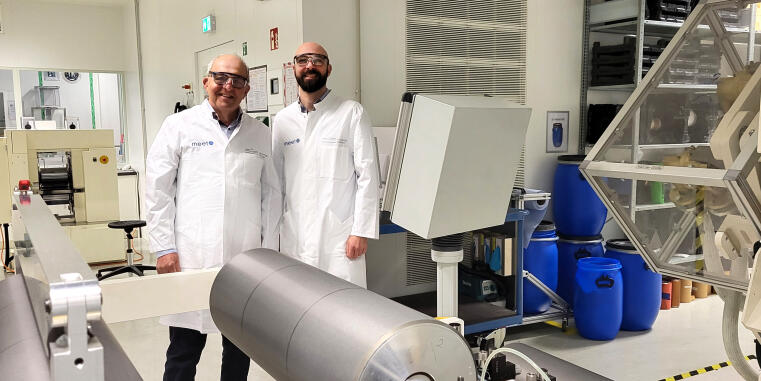
War es zu der Zeit etwas Besonderes, dass eine Forschungseinrichtung eine eigene Produktionslinie aufgebaut hat?
Gerhard Hörpel: Definitiv. Zu der Zeit haben eher technische Universitäten mit ingenieurswissenschaftlichem Schwerpunkt mit solchen Anlagen gearbeitet, um die entsprechenden Maschinen und Einzelprozesse weiterzuentwickeln. Das war nicht unser Ansinnen. Ganz platt gesagt: Wir haben eine Batterielinie aufgebaut, die funktionieren sollte. Unser Fokus lag darauf, mit einer durchgängigen Produktionsstruktur Materialien zu testen und dafür Zellen herzustellen.
Markus Börner: Und das tut er heute noch. Die Anforderungen an Batterien steigen stetig. Sie sollen leistungsstark, langlebig, sicher und kostengünstig sein, aber auch nachhaltig und recycelbar. All diese Parameter zu erforschen, wäre ohne Batterielinie gar nicht möglich. Sie ist unser Herzstück und läuft seit zehn Jahren wie ein Uhrwerk.
Gibt es ein bestimmtes Highlight aus der damaligen Zeit, das Ihnen im Gedächtnis geblieben ist?
Gerhard Hörpel: Als wir die ersten Pouch-Zellen herstellen konnten und sich die ganze Arbeit ausbezahlt hat, war das natürlich ein toller Moment. Durch die enge Zusammenarbeit mit unseren japanischen Partner*innen haben wir uns nicht nur fachlich enorm weiterentwickelt, sondern auch viele kulturelle Besonderheiten entdeckt, die unseren Blick auf dieses faszinierende Land erweitert haben. In der Planungsphase sind wir häufiger nach Japan gereist. Dort habe ich unter anderem gelernt, dass es in Japan üblich ist, sich das Bier nicht selbst einzuschenken – diese Aufgabe übernimmt der Sitznachbar. Gleichzeitig muss ich darauf achten, dass auch mein anderer Sitznachbar stets gut versorgt ist. Das sind Erinnerungen, die ich in meinem Leben nicht mehr vergessen werde.
Und wie hat sich die Batterielinie seit ihren Anfängen weiterentwickelt?
Markus Börner: Wir haben immer wieder Elemente ausgetauscht, um sicherzustellen, dass unsere Batterielinie dem neuesten Stand der Technik entspricht. Ein neuer Kalander ermöglicht es uns zum Beispiel, die Temperatur beim Kalandrieren der Elektroden zu variieren. Er verfügt außerdem über eine verbesserte Federung. Ganz aktuell beschäftigt uns die Rückverfolgbarkeit entlang der gesamten Prozesskette. Die zunehmende Digitalisierung in der Batteriezellproduktion erlaubt es uns, jedes Material und jede Elektrode bis ins kleinste Detail zurückverfolgen zu können. Das hilft uns enorm dabei, Ergebnisse unserer Analysen auf einzelne Komponenten oder Materialzusammensetzungen zurückzuführen.
Wie sieht die Zukunft aus?
Markus Börner: Der Markt an Batterietechnologien wird sich weiter ausdifferenzieren. Das bedeutet: Es gibt nicht die eine Zelle für alle Anwendungen, aber für alle Anwendungen eine spezielle Zelle. Ein Beispiel ist die Natrium-Ionen-Batterie. Ihre Produktionsschritte ähneln denen der Lithium-Ionen-Batterie, sodass wir auf unsere bestehende Infrastruktur zurückgreifen können. Es muss allerdings sichergestellt sein, dass es keine Querkontamination gibt. Eine modulare Lösung wäre denkbar, bei der bestimmte Elemente der Batterielinie ausgetauscht und wirklich nur für eine Batterieart eingesetzt werden.
Um uns für die Produktionsprozesse von Post-Lithium-Ionen-Batterien zu rüsten, die deutlich andere Schritte in der Herstellung erfordern, haben wir vor wenigen Jahren außerdem eine zweite Pilotlinie im MEET installiert: Eine acht Meter lange Spezialanlage, mit der wir zunächst mehrlagige Lithium-Metall-Batteriezellen produzieren können. Sie ist die perfekte Ergänzung für unsere bestehende Pilotlinie für Lithium-Ionen-Batterien.